When Dr. Stephen DeFelice coined the term "Nutraceutical"in 1989, he likely never imagined the word would come to represent such a large and fast-growing industry segment. Herbal products, vitamin/dietary supplements, fibers, phytonutrients, pre- and pro-biotics and protein/amino acids can all be found online and on shelving, and business is booming. Increasing numbers of health-conscious consumers, social media platforms touting various dietary health regimens, and pandemic-driven searches for products to strengthen immune system response have pushed nutraceutical industry growth and is expected to continue for the foreseeable future.
While great news for business, manufacturers face a continuing challenge: maintaining both high throughput and repeatable nutraceutical product quality in processing with what are characteristically very fine powders... "sluggish" ingredients that tend not to flow freely.
Obviously, the choices made in sifting or screening technologies used to prepare these very fine particulate ingredients will have a considerable impact on key criteria – throughput and quality -- in terms of capacity, uptime and downstream productivity. These choices should be based on considerations that include:
- Appropriate capacities and throughput
- Appropriate design for specific process lines
- Suitability for batch and/or continuous blending
- Ease of access/speed for cleaning and maintenance
- Energy consumption
- Durability and longevity
- Adherence to sanitary standards as required
- Availability of pre-purchase testing and post-purchase technical support
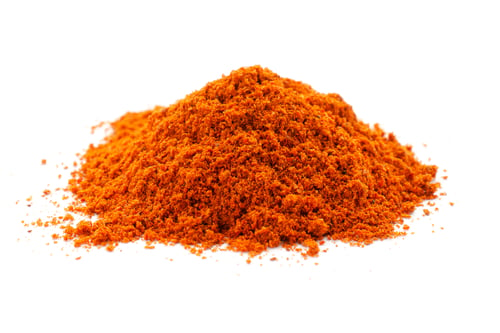
Sifting and Screening Options for Nutraceutical Manufacturing
Given that we are discussing "sluggish" powders possessed of a very high angle of repose, the whole challenge is to transfer the precise energy necessary which would allow the good product material particles to pass through the screens as efficiently as possible.
In the case of nutraceuticals, another clear goal is the removal of all possible contaminants, including products of previous processing: bits of paper and bag liners, closures, scale from processing equipment upstream, etc., that ends up in the product fraction.
Whether a particular ingredient requires sifting/screening, scalping, de-lumping or conditioning to create a homogeneous powder ready for blending, manufacturers generally have a choice of these innovative technologies.
Vibrational screening - a flat deck, circular vibratory unit with screens mounted atop a motor that drives the vibratory action at amplitudes appropriate for the material to be sifted. Kason VIBROSCREEN® Circular Vibratory Screeners and Separators utilize the latest technology and are available in a host of sizes and configurations to match any nutraceutical manufacturing challenge.
Centrifugal sifters - a horizontal cylinder in which a paddle assembly spins and flings the material against a stationary cylindrical screen basket. The mechanical advantage here is that this technology actually fluidizes the ingredient, imparting more energy into the particles as they arrive at the screen hole openings increasing the number of particles passing through. Kason CENTRI-SIFTER® Centrifugal Sifters and Separators are versatile, high-capacity, compact workhorses with features ideal for this application.
Key Considerations Driving Technology Choices
- Capacity/throughput - A primary question for most nutraceutical manufacturers is capacity/throughput. For example, "I need to produce X pounds of this powder per hour." Variables impacting screening throughput include design efficiency, mechanical efficiency, ease of cleaning and the ability to customize loading/unloading.
- Mix quality - This is balanced by the quality of product produced: the "efficacy of the cut." A given ingredient must be optimal for the final product so that it looks a certain way, dissolves a certain way or encapsulates a certain way. The degree to which screening contributes to ultimate product quality while maintaining throughput is a critical consideration.
- Cleaning/maintenance - Cleaning and maintenance are other factors in choosing the right sifter, especially when having to quickly go from one batch to another. The VIBROSCREEN units open with a simple clamp ring, either manually or with tools, exposing the screen for inspection or replacement in a matter of minutes. The CENTRI-SIFTER is even simpler, with a removable endplate offering full access to slide out the screen basket and internal parts. Centrifugal sifter screens are power horses, reducing product caking that might slow production. Kason's Screen Replacement Program brings greater assurance of continuous operation, including compatibility with other manufacturers' equipment.
- Management of difficult materials - To achieve capacity/throughput and desired mix consistency with sluggish materials, a Kason VIBRO-SCREEN or any flat deck vibratory unit should push as much energy into the batch as possible. This specialized process requires selecting the appropriate motor plus the appropriate horizontal and vertical amplitudes. Typically, with nutraceuticals, even if they are fine powders, Kason recommends an anti-blinding device, either Kleen Screen Rings or Anti-Blinding Ball Tray assembly. The anti-blinding device adds additional energy into the unit by hitting the bottom of the working screen, allowing particles to separate and move across the screen easily.
Centrifugal sifters, such as Kason CENTRI-SIFTERS, are also a great choice for sluggish materials. As a CENTRI-SIFTER processes sluggish material, the paddle assembly fluidizes it, adding energy to the particles so they separate from the larger mass. This makes the mixture become "airborne" within the sifter and have a better chance of finding the screen hole openings surrounding them (as opposed to a cake of material just bouncing on a vibratory screener).
Pre-purchase Engineering Support and Try-Before-You-Buy Rental Options
Hardware is one thing. However, selecting the optimal sifting/screening technology for specific nutraceutical applications has proven to be highly dependent on pre-sale engineering expertise. While many manufacturers offer testing to help determine if a given sifter will meet a particular demand, Kason's Materials Test Lab is staffed by veteran process engineers as well as highly trained technicians. The difference can be crucial. With highly trained personnel managing the lab and performing the tests, the customer is assured that staff with the requisite problem-solving backgrounds are involved to solve whatever challenges and difficulties are revealed.
Testing is free. For applications involving hazardous materials or confidential formulations, Kason can put the appropriate rental unit in the customer's facility to prove the application.
Example: Cannabis processors have used their experience to develop techniques that increase the quality and efficiency of their extraction processing operations for the production of edibles, smokables and topical ointments. In one case, a cannabis company, challenged by the need to remove very fine particles of trichome off the cannabis bud for further processing, rented a Kason CENTRI-SIFTER with very fine mesh screens to adapt it to their process.
Result: The customer was able to accomplish the task without encountering screen fouling simply by using their ingenuity and familiarity with their product. The success provided proof of concept and led to multiple sifter installations to solve their customer requirements.
Experienced engineers listening first and acting on what they hear make all the difference in moving an application process forward. Kason offers a complete selection of screening and processing equipment ideal for nutraceutical applications, from off-the-shelf units to complete, built-to-spec high-capacity systems. We also bring more than 50 years of engineering excellence, innovative design and practical application expertise. Kason leads the way for performance, dependability, ease of maintenance and aftermarket support. When you're ready to talk to an application specialist about your nutraceutical sifting process, fill out our contact form or call 973-467-8140.